How Are Fire Dampers Tested?
Everyone knows fire dampers have to be fire tested in order to become CE marked, but what exactly does this testing involve?
Legislation
Fire dampers are subjected to fire testing as prescribed by EN 1366-2, this full scale furnace test is arguably more severe than any fire likely to be seen in the real world, however it is this severity which ensures any damper which satisfies it can be relied upon to perform in a real fire scenario.
Contact Us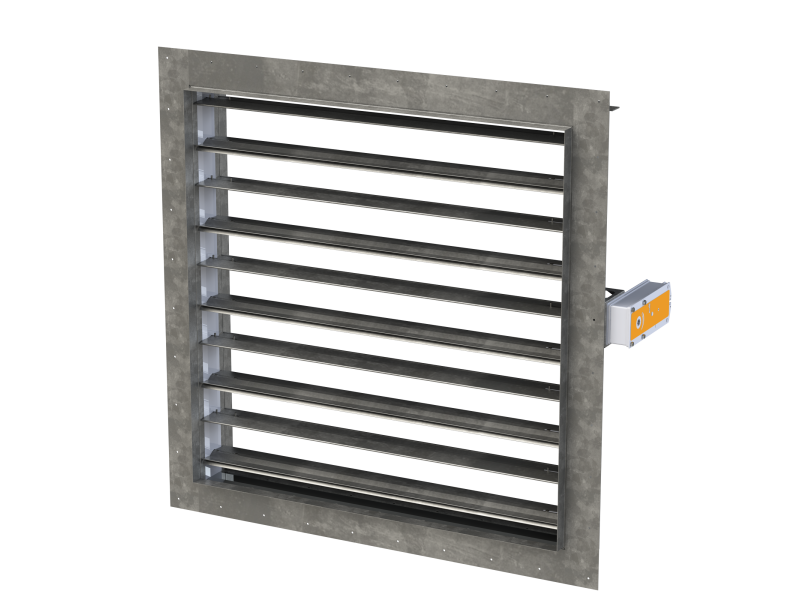
Performance Test
Testing against EN 1366-2 demands that a sample damper is tested in the substrate it is to be certified for, this could be a concrete floor slab, flexible (plasterboard) wall, or a proprietary system such as a fire curtain or shaft wall. Test houses such as BRE, Applus or Gryfitlab will build a sample construction of at-least 3m x 3m within a large steel frame. Once the damper is installed as per the damper manufacturer’s instructions within the substrate, the entire assembly is craned into position on a gas fired furnace, capable of reaching temperatures approaching 1200°C. A plenum box is then connected to the unexposed side of the damper, serving as the connection point between the damper itself and ducting.
Once the pre-test formalities are complete, such as 50 successful open and close cycles and signing off of the installation by the manufacturer’s witnessing representative, the equipment is readied for testing. High temperature fans are set to draw a constant 0.15 m/s through the damper, sensors are verified to be working and then the furnace is lit. Fire dampers always start a test in the fully open position, and have a maximum of 2 minutes to close after the test commences. Given the nature of fire testing, visual verification of closure is not reliable, therefore closure is verified by monitoring of the under-pressure within the connection plenum, which needs to increase by at-least 50 Pa over a 5 second time period.
Assuming the damper closes within the allowed time, fans will be set to maintain an underpressure of 300 Pa within the plenum, and leakage readings through the damper will start being taken, although they only have consequence once 5 minutes have passed to allow stabilisation. All being well, the test will then proceed for the time period requested by the manufacturer. In order to apply extended field of application (EXAP) rules, manufacturers will normally request the test duration is 10% more than the duration by which dampers are marketed, i.e. at HVC we will normally test a 2 hour rated damper for 132 minutes.
Monitoring Performance Criteria
Throughout the test duration, there are two main performance criteria which are monitored; leakage and installation stability. Leakage through the damper should not exceed 360 m3/hr/m2 for ‘E’ rated dampers, or 200 m3/hr/m2 for ‘ES’ or ‘EIS’ rated dampers, and if EXAP rules are to be applied the damper must not get within 10% of these volumes. Installation stability looks not only for whether the installation remains intact, but also whether anything on the unexposed side (i.e. not within the furnace) ignites for more than x seconds, should any of these rules be broken, the test will be considered a failure.
If all goes well and the test is successful, then the result can be factored into classification and EXAP documents, ultimately feeding into the certificate of constancy of performance from which manufacturers can draw up their declaration of performance, allowing them to market their damper.
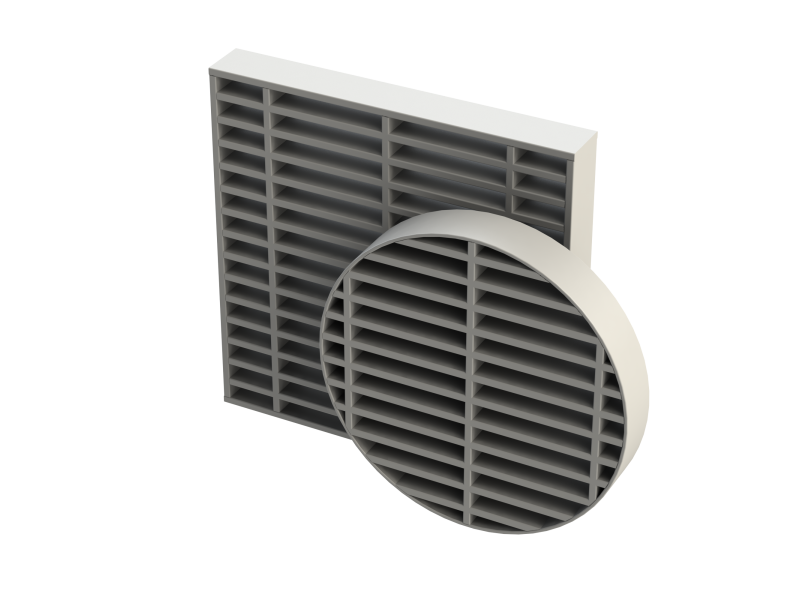
-
Get in Touch with Any Questions
Get in Touch with Any Questions
If you have any questions about how fire dampers are tested, please contact us today.